Finalmente ho il tempo di aggiornare la discussione.
Ho passato l'ultima settimana tra lezioni e battere la testa sulla tastiera perchè matlab non voleva collaborare.
Allora, riprendendo da dove eravamo rimasti:
Pressione in camera di CombustioneLa pressione in camera di combustione è un parametro fondamentale per il dimensionamento del motore in quanto è proprio questa pressione che "genera" la spinta.
Si può dimostrare che allo stadio di equilibrio tra massa prodotta dalla combustione del propellente e quella che esce dall'ugello, la pressione in camera di combustione assume questa forma.
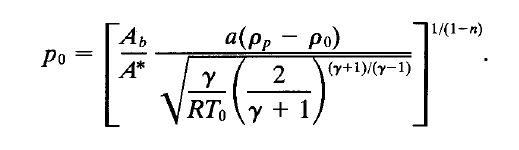
Arrivare a questa relazione non è difficile, bisogna considerare infatti la quantità di gas prodotte dalla combustione del propellente e la portata di quella che esce dall'ugello strozzato.
Per il Burn Rate, ovvero la velocità alla quale brucia il combustibile si usa una formula empirica:
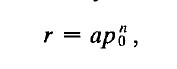
Dove P0 è proprio la pressione in camera di combustione, a ed n sono delle costanti sperimentali dipendenti dalla pressione e dal propellente e r è la velocità di combustione in mm/s (qualora P0 sia in Mpa).
Tralasciando passaggi noiosi si giunge ad un equazione differenziale dell'andamento della pressione. Ponendo a zero la derivata della pressione nel tempo ( e quindi considerando il così detto steady state), si ottiene la formula messa poco prima.
A questo punto possiamo notare il termine Ab/A*, che essenzialmente è l'unica cosa che varia nella formula della pressione, quindi è bene capire cosa rappresenti.
Ab è la superficie che sta bruciando di combustibile, in particolare la superficie istantanea, mentre A* è l'area di gola del''ugello, che una volta definita è fissa.
Per calcolare la superficie istantanea che che sta bruciando possiamo partire dalla superficie libera (non inibita dalla combustione) del propellente a t=0 e variarla in funzione del tempo essendo x=r*t la Web Regression, ovvero essendo r una velocità di combustione possiamo ottenere quanti mm bruciano dopo tot secondi.
Si definisce quindi il parametro Kn= Ab/Ac* in modo da poterlo plottare in funzione della web regression.
Tutto questo può sembrare molto complicato, perchè in effetti è un processo non risolvibile in forma chiusa, con una bella equazione. Questo perchè il Web regression dipende da r, ma r dipende dalla pressione, che a sua volta dipende da Ab/Ac*, ma abbiamo detto che Ab dipende da r e Ac non la conosciamo ancora in quanto non si può dare a caso.
Quindi dopo tutto questo rigiro di parole si giunge alla conclusione che questo sia un processo iterativo.
Nei processi iterativi si da una stima iniziale di un valore e poi ad ogni iterazione si ricalcola con le formule avvicinandoci sempre più alla soluzione (sempre che i cicli non vadano in loop senza trovarne il motivo

).
Si capisce anche che ci vuole un dato iniziale da cui partire, una scelta di progetto, un constrain.
Nel mio caso i vincoli che sceglie il progettista sono le dimensioni del propellente (tutti i parametri del propellente sono noti), se ci sono superfici inibite dalla combustione ed il numero di segmenti, e la pressione massima che vogliamo raggiungere in camera di combustione. Questa può essere dettata da limiti strutturali, non vogliamo che nel nostro motore si raggiungessero pressioni più elevate di quelle per cui è progettato.
Solitamente quando si progetta un motore per un razzo si ha ben in mente il quadro generale della missione, per esempio la capacità di portare in LEO venti tonnellate di payload. Siccome io sto per ora progettando un motore, senza ancora pensare al razzo, per fare test sul motore e attestare il fatto che la progettazione è stata buona, la spinta non è un mio dato di input ma bensì un output.
Su Matlab ho quindi implementato un processo iterativo, non dei migliori in quanto è lento, ma funziona. Ho sperimentato anche con delle interfacce utente e sono riuscito ad ottenere una cosa passabile, che via via migliorerò. I risultati sono stati comparati con quelli dello spreadsheet proposto da Nakka e sono molto simili, le diversità stanno probabilmente in alcune costanti del propellente e anche nel fatto che non ho considerato l'erosive burning dato dall'alta velocità dei gas in camera di combustione. Tuttavia per un dimensionamento preliminare è più che adeguato, in modo da evitare spiacevoli sorprese.
Ecco come appare la schermata dopo aver fatto i conti:

La parte finale della curva della pressione, e quindi anche della spinta, deve essere calcolata con un'altra equazione in quanto non vale più l'ipotesi di steady state. O meglio va risolta l'equazione differenziale e si ottiene per questo ultimo tratto un decremento esponenziale. Per ora ho usato il volume della camera di combustione pari a quello del propellente, in realtà non è vero, dovrà essere leggermente più grossa per alloggiare il propellente e lo spazio tra i vari segmenti. Tuttavia devo ancora capire come mettere una seconda finestra nell'interfaccia grafica perchè in quella di ora ho finito lo spazio per i dati di input.
Piano piano la migliorerò.
Per quanto riguarda i materiali da utilizzare per l'ugello, per fare i primi test basterà probabilmente un comune acciaio inox, il burn time è molto breve e nonostante l'elevata temperatura, a quanto dicono i test report di Nakka, non si apprezza eccessiva usura dell'ugello. Lui lo ha fatto in 1810 se non erro.
Per il corpo ci sono varie opzioni, se si vuole usare l'alluminio bisognerà mettere uno strato di isolante termico (anche carta da pacchi arrotolata e ben pressata, tanto una volta acceso il motore la camera di combustione è priva di ossigeno), per evitare che l'alluminio si indebolisca con la temperatura fino a non riuscire a resistere alla pressione interna. Se si volesse fare d'acciaio non credo ci siano problemi visto il maggior punto di fusione e una yeld strenght molto più elevata. Con l'aisi 304 anche a 600 gradi avrei un fattore di sicurezza maggiore di 2-3. In ogni caso farò qualche calcolo di trasmissione del calore e saprò meglio cosa utilizzare.
Il bulkhead verrà fatto di "sicurezza" in modo che scoppi prima quello ( si spezzano le viti di fissaggio o qualcosa del genre), prima che arrivi a scoppiare la camera di combustione.
Anche per questo post è tutto, prossimamente mi farò vivo con degli aggiornamenti. Se avete consigli,critiche o domande non abbiate timore di scrivere, questo è prima di tutto un esperimento didattico.